The Importance Of 5s Lean Manufacturing
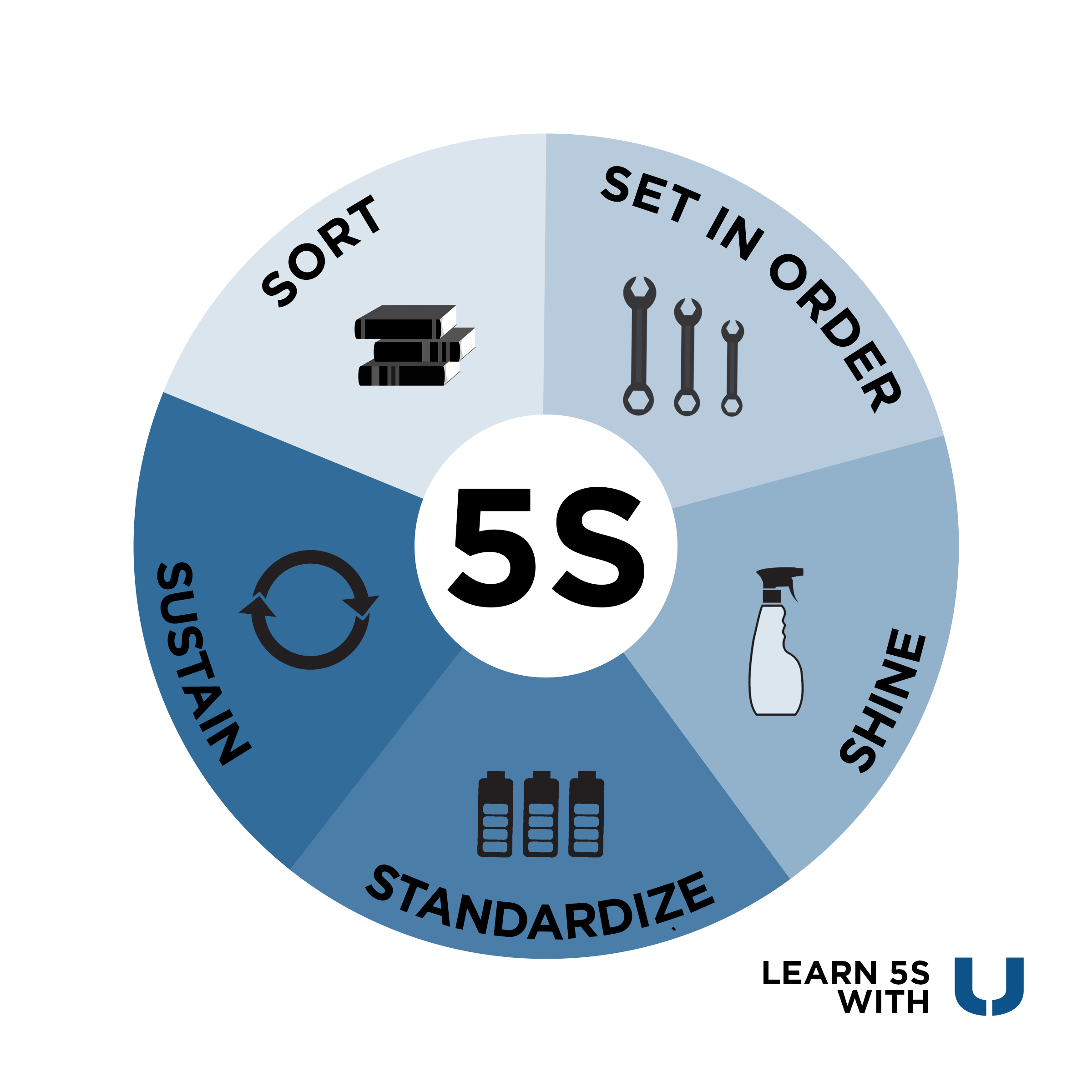
The Importance Of 5s Lean Manufacturing Why is 5s important in manufacturing? while 5s was first developed in the context of the automotive industry, it is now widely considered an essential step for any lean manufacturing program, regardless of industry. embedding 5s as part of daily tasks within your company means much more than improved organization, sustained cleaning routines. The 5s system is part of toyota’s lean manufacturing methodology designed to reduce waste within a facility. 5s is typically the first step towards eliminating waste from manufacturing processes and eventually leads to improving bottom line results. 5s is a foundation of kaizen, which is the practice of continuous improvement based on certain.

What Is 5s Lean Manufacturing Simplified Clients First Acumatica The 5s quality tool is derived from five japanese terms beginning with the letter "s" used to create a workplace suited for visual control and lean production. the pillars of 5s are simple to learn and important to implement: seiri: to separate needed tools, parts, and instructions from unneeded materials and to remove the unneeded ones. The 5 pillars of 5s lean manufacturing. 1. sort. remove all items not needed, leaving only the bare essentials. sorting saves time, space, and labor costs while enhancing productivity. 2. set in order. arrange items, so they are easy to use; label items so anyone can find them or put them back in the right location. The 5s in lean manufacturing is meant to maintain a safe, organized, and efficient workplace. though the japanese team at toyota has been credited with developing the 5s technique, the original concept was developed by ford and was called the cando system. it stood for cleaning up, arranging, neatness, discipline, and ongoing improvement. 5s is a structured methodology designed to create and maintain a well organized, clean, and efficient workplace. originating from japan, it is one of the foundational tools in lean manufacturing, focusing on eliminating waste and improving operational efficiency. the five steps of 5s—sort, set in order, shine, standardize, and sustain.

5s Lean Tools Techniques Tradesafe The 5s in lean manufacturing is meant to maintain a safe, organized, and efficient workplace. though the japanese team at toyota has been credited with developing the 5s technique, the original concept was developed by ford and was called the cando system. it stood for cleaning up, arranging, neatness, discipline, and ongoing improvement. 5s is a structured methodology designed to create and maintain a well organized, clean, and efficient workplace. originating from japan, it is one of the foundational tools in lean manufacturing, focusing on eliminating waste and improving operational efficiency. the five steps of 5s—sort, set in order, shine, standardize, and sustain. In the field of lean manufacturing, fives has been widely used. the tools for lean manufacturing have become the best in the business world and are widely used. 5s increases productivity, reduces costs and enhances quality. often the lean program focuses on these objectives, and the human factor does not appear. the security of employees is. 5s is a lean principle aimed at reducing waste and being more efficient in how things are done. the manufacturing and production methodology is a systematic approach to organizing and managing the workplace. each “s” in 5s refers to different principles, which are sort (seri), set in order (seiton), shine (seiso), and standardize (seiketsu).

What Is The Meaning Of 5s Principle At Heather Carlson Blog In the field of lean manufacturing, fives has been widely used. the tools for lean manufacturing have become the best in the business world and are widely used. 5s increases productivity, reduces costs and enhances quality. often the lean program focuses on these objectives, and the human factor does not appear. the security of employees is. 5s is a lean principle aimed at reducing waste and being more efficient in how things are done. the manufacturing and production methodology is a systematic approach to organizing and managing the workplace. each “s” in 5s refers to different principles, which are sort (seri), set in order (seiton), shine (seiso), and standardize (seiketsu).
Comments are closed.