Mig Welding Technique For Thin Metal
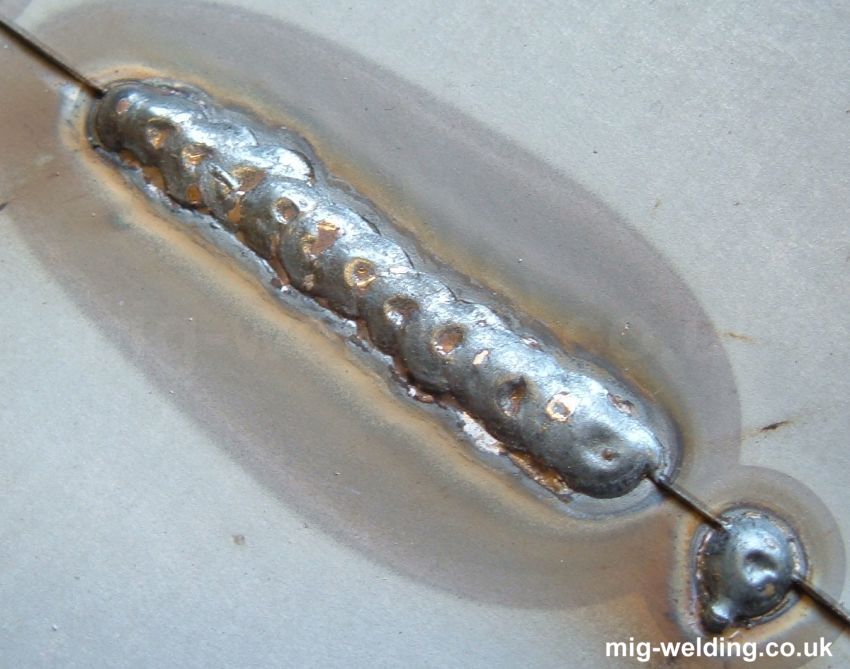
Mig Welding Technique For Thin Metal Mig welding simplifies the feeding of filler metal, making the welder’s job easier. while the specific material may not be critical, the form of the filler metal is important when working with thin sheet metal. 3. adjust the torch angle. modifying the torch angle during mig welding significantly helps prevent burn throughs. To weld thin stock successfully, use a small diameter tungsten electrode like 0.020, 0.040, and 1 16 in. large diameter tungsten electrodes require higher amperage to start the arc, leading to warping or burning of the material. grind the tungsten tip to a sharp point to weld steel, and use either er70s 2 filler metal or a silicon bronze rod.

How To Mig Weld Super Thin Metal With No Warping Youtube Technique for thin metal. the way around this is to weld in short pulses, allowing a second or less between pulses for the steel to cool down. in the video i've left about a second between pulses. these days i'll normally leave less than half a second. the longer you leave the more chance you'll have of cold joints and pinholes between the welds. To weld thin metal, choose an appropriate process (tig or mig with low amperage), use a smaller diameter wire or filler rod, and adjust travel speed to prevent burn through. employ a pulsing technique, stitch welding, or tack welds to manage heat and allow cooling periods between welds to minimize warping. when most people think about welding. Maintain a short arc length: keep the arc length as short as possible without touching the metal. a shorter arc length helps to minimize heat input and reduce the risk of burn through. use a push technique: when mig welding thin sheet metal, it’s generally recommended to use a push technique. In this video i demonstrate how to set up your mig welder so you can weld thin sheet metal. we also showed in this video how to make your pattern, fit and we.

How To Mig Weld Thick Steel To Thin Steel Youtube Maintain a short arc length: keep the arc length as short as possible without touching the metal. a shorter arc length helps to minimize heat input and reduce the risk of burn through. use a push technique: when mig welding thin sheet metal, it’s generally recommended to use a push technique. In this video i demonstrate how to set up your mig welder so you can weld thin sheet metal. we also showed in this video how to make your pattern, fit and we. In this approach, heat a small plates’ segment you want to connect and then let the weld pool cool completely. don’t try to fill in the joint all at once. doing so forms a hole in the workpiece. image credit: kinganowak 22, pixabay. this procedure has a high penetration of materials and metal deposition. The welding parameters vary for each of the recommended wire diameters and also depend on how thin the material is. for example, both 0.024 and 0.30 inch solid wires can be used to weld 24 gauge material using a welding current of 30 to 50 amps and travel speeds of 10 to 20 inches per minute (ipm). the voltage and wire feed speed vary though.
Comments are closed.