Lean 5s Six Sigma Safety Science
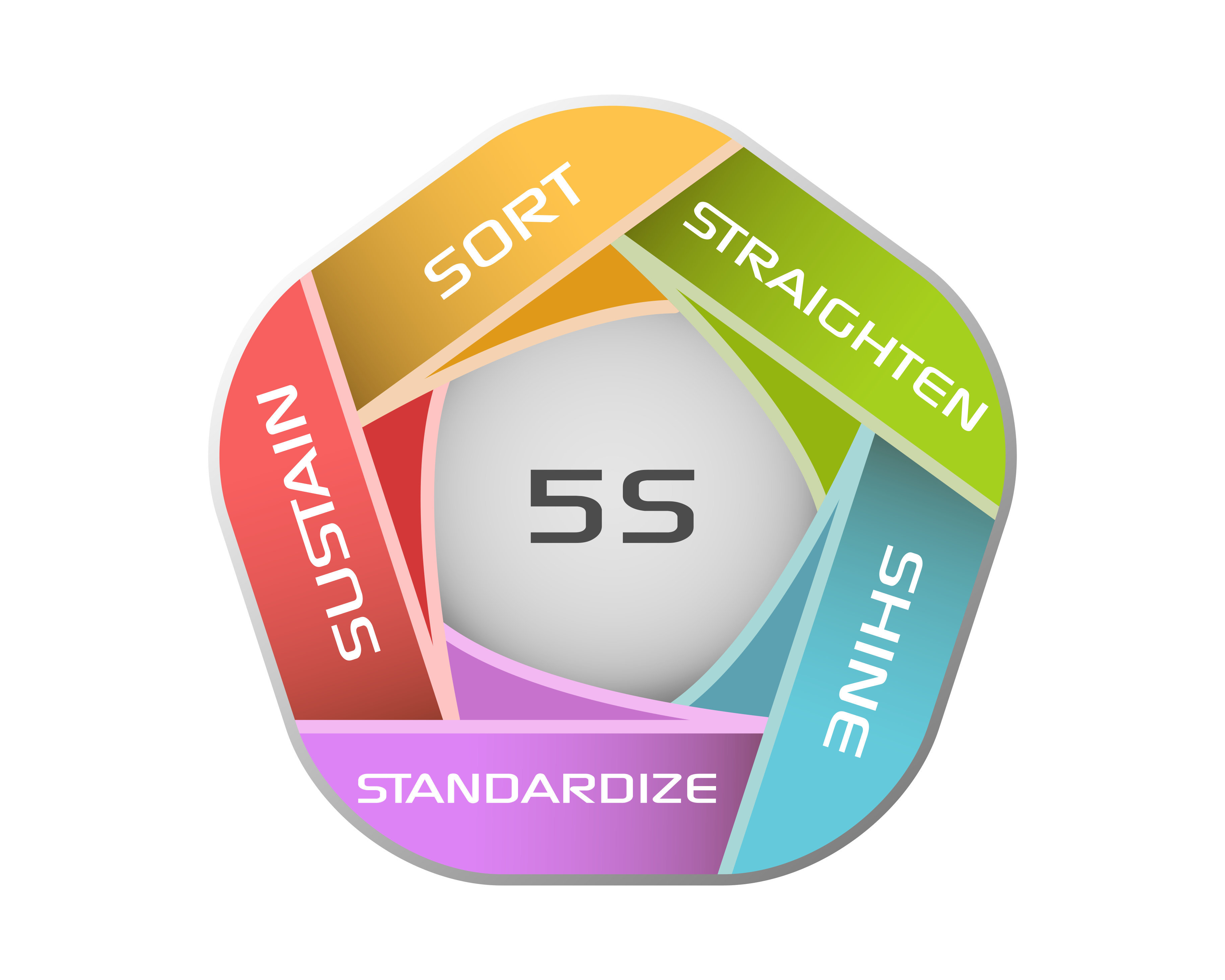
Lean 5s Six Sigma Safety Science 6s lean: 5s safety. 6s (otherwise known as 5s safety) is a system that aims to promote and sustain a high level of productivity and safety throughout a workspace. while adhering to the 5s principle of sort, set in order, shine, standardize, and sustain, the 6s method adds the concept of safety. 6 s lean not only helps organizations promote. 5s is a structured methodology designed to create and maintain a well organized, clean, and efficient workplace. originating from japan, it is one of the foundational tools in lean manufacturing, focusing on eliminating waste and improving operational efficiency. the five steps of 5s—sort, set in order, shine, standardize, and sustain.

Lean 5s Six Sigma Safety Science Lean manufacturing is a systematic method focussing on the improvement of industrial processes. 5s is a lean manufacturing term, referring to 5 japanse words. straighten : identify the best location for each item, placing essential items in assigned locations. all non essential items are removed from the work area in question. Quality glossary definition: five s’s (5s) 5s is defined as a methodology that results in a workplace that is clean, uncluttered, safe, and well organized to help reduce waste and optimize productivity. it's designed to help build a quality work environment, both physically and mentally. the 5s philosophy applies in any work area suited for. Adherence to 5s standards is considered the foundation of total productive maintenance (tpm) and an integral part of the toyota production system (tps). 5s also creates a stable platform from which kaizen activities can be launched. the bottom line 5s is a low investment, high impact lean manufacturing tool that is predicated on people. 5s is a five step organizing technique that helps organizations design and maintain intuitive workspaces. the overarching aim of 5s is to identify, change, and eradicate process elements that fail to add value or, worse, actively decrease value. the methodology has its roots in the 1930s when auto manufacturers created the principles to improve.
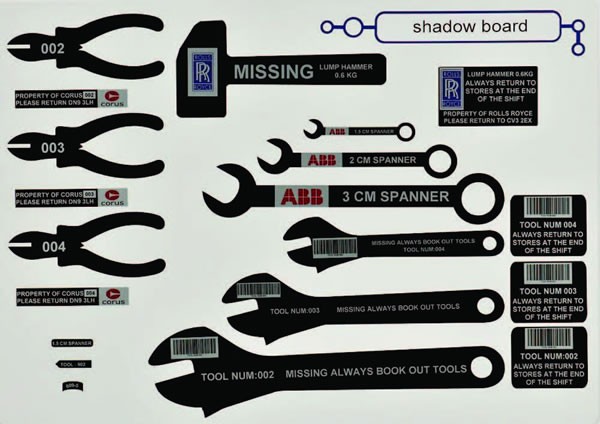
Lean вђ 5s вђ Six Sigma Safety Science Adherence to 5s standards is considered the foundation of total productive maintenance (tpm) and an integral part of the toyota production system (tps). 5s also creates a stable platform from which kaizen activities can be launched. the bottom line 5s is a low investment, high impact lean manufacturing tool that is predicated on people. 5s is a five step organizing technique that helps organizations design and maintain intuitive workspaces. the overarching aim of 5s is to identify, change, and eradicate process elements that fail to add value or, worse, actively decrease value. the methodology has its roots in the 1930s when auto manufacturers created the principles to improve. Implementation of a visual workplace is a way to attain the common goals of lean six sigma, such as reducing the 8 wastes and improving quality. the visual workplace that 5s methodology is meant to enable has roots going back centuries. however, the current form is usually considered to have been part of the evolution of the toyota production. 5s is a five step organization technique to create and maintain an intuitive workspace. the five steps are: sort – remove unnecessary items from the workplace. set in order – arrange items so they are easily accessible. shine – clean the work area so it is neat and tidy. standardize – set standards for a consistently organized workplace.
Comments are closed.