How Work Order Management Ensures Maintenance Success
How Work Order Management Ensures Maintenance Success Fmx 3. maintenance manager approves the work order. the next step is processing and approving the request. typically, processing is performed with software and overseen by a maintenance manager. if the maintenance requested requires any special parts or equipment, those items should be obtained in this step. 4. Work order management (wom) is a systematic approach to organizing and controlling every aspect of maintenance tasks – from initiation to completion. it includes defining the work scope, scheduling, assigning tasks, executing work, and recording outcomes. wom prioritizes tasks, optimizes resources, and executes maintenance activities.
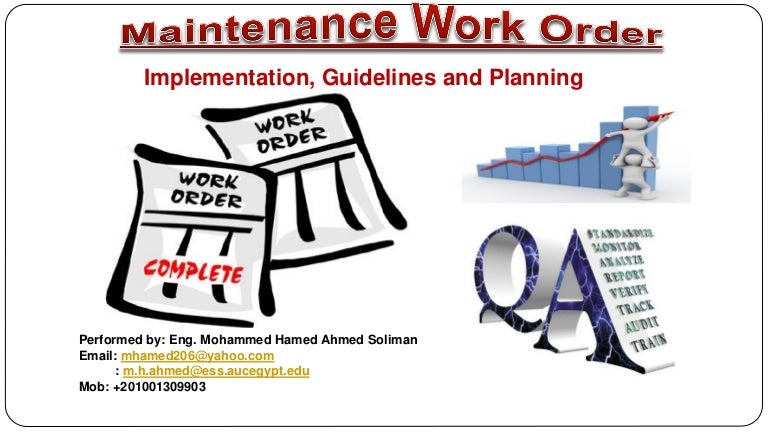
How Work Order Management Ensures Maintenance Success New Guide Vrogue Schedule tasks: assign tasks to your maintenance team based on their priority, ensuring they address high priority tasks first. monitor progress: use a work order management system to track task completion and monitor workflows. adjust as needed: review the prioritization process regularly. A work order is a document that outlines all the information needed to complete an installation, preventive maintenance, or similar task. they often include details like who authorized the job and who the job is assigned to, what the job entails, what assets are required, insight into the job’s service history, and information about any other expectations regarding the job. 5. complete and close out the work order. once assigned, the technician can focus on closing out the work order. the assigned technician should adhere to any safety protocols and follow any guidelines in place for repairing equipment. if possible, ensure the technician logs their work in your work order system. 6. Step 1: task identification. the first stage of the work order management process is identifying an issue that needs resolution. in some cases, this will be a planned identification, where the maintenance department generates work orders for tasks that they know they’ll have to complete.
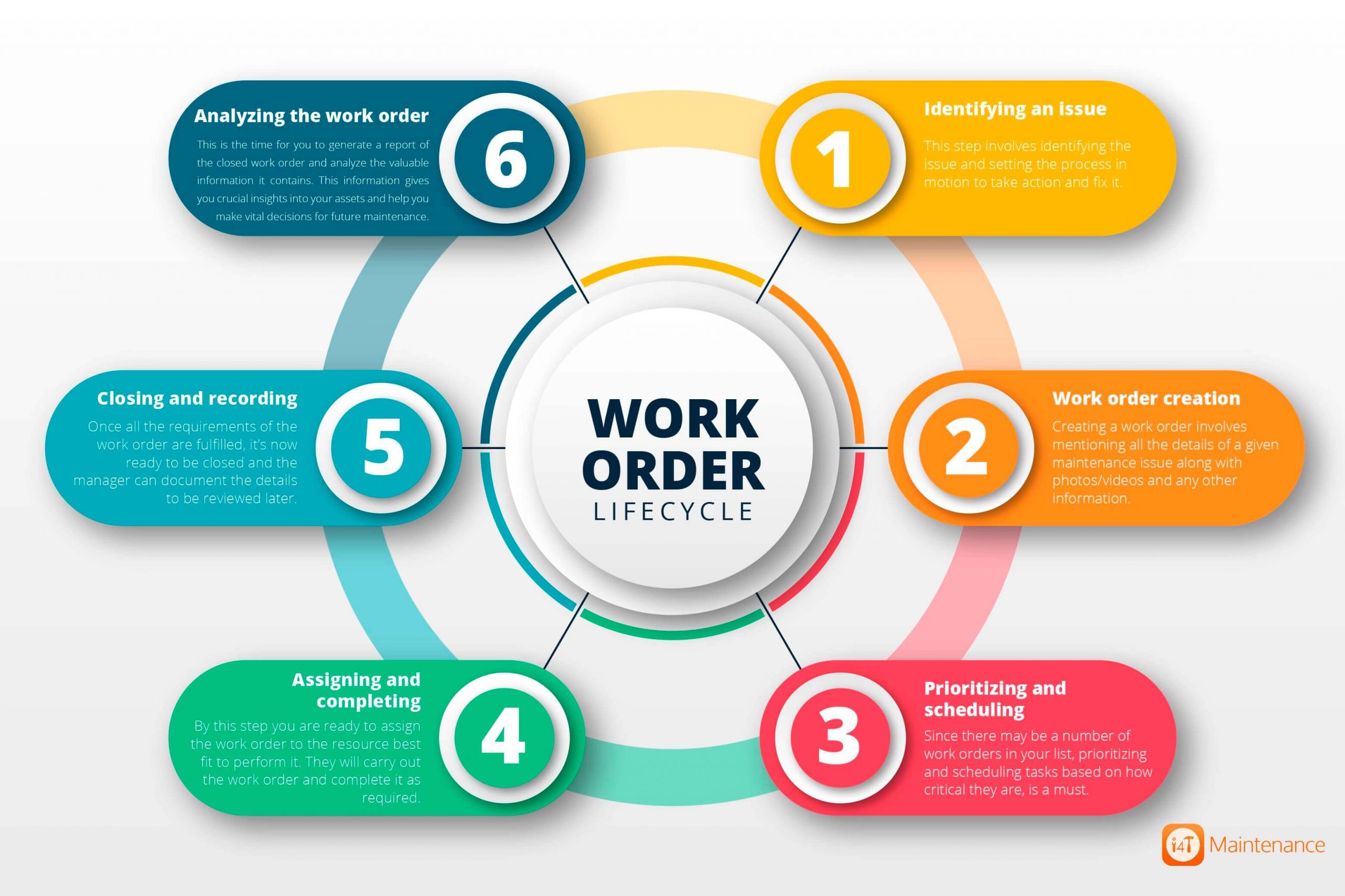
Anatomy Of A Work Order Management Process Infographi Vrogue Co 5. complete and close out the work order. once assigned, the technician can focus on closing out the work order. the assigned technician should adhere to any safety protocols and follow any guidelines in place for repairing equipment. if possible, ensure the technician logs their work in your work order system. 6. Step 1: task identification. the first stage of the work order management process is identifying an issue that needs resolution. in some cases, this will be a planned identification, where the maintenance department generates work orders for tasks that they know they’ll have to complete. The maintenance manager also needs to take into consideration an efficient distribution of workload for his team. best practice: fill in the gaps left by requesters when necessary. when a valid maintenance request is approved to become a work order, the requester only knows so much about the asset and job in question. 5. tracking and reporting. mastering the art of tracking and reporting is essential for the smooth operation of work order management systems in manufacturing. maintenance crews can access instant task updates by observing and analyzing work orders, effectively prioritizing critical repairs.
Comments are closed.