Brazing Manufacturing Process At Freddy Frederick Blog
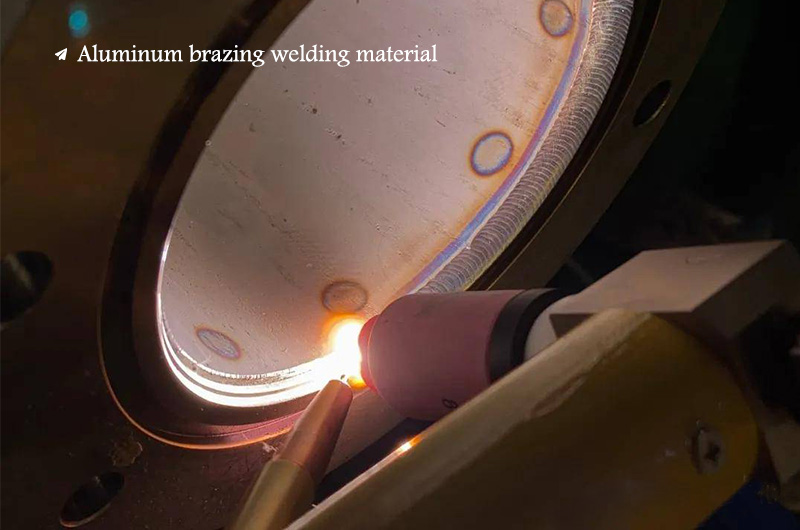
Brazing Manufacturing Process At Freddy Frederick Blog Web brazing process step 1: brazing, as we’ve seen, uses the principle of capillary action to distribute the molten. web brazing is a process to join two or metal parts using a filler metal with a lower melting point which flows into. brazing manufacturing process. from . Begin heating the tube by applying the flame perpendicular to a point just adjacent to the fitting, moving the flame and heating completely around the tube. move to the fitting while still holding the flame at a 90 degree angle and work around the fitting. 5. apply the brazing alloy.

Brazing Manufacturing Process At Freddy Frederick Blog Brazing is also a common way that metallurgists make fine jewelry. in order for brazing to work properly, the base metals need to be clean enough for the filler metal to flow freely over them without any interference. achieving this cleanliness means the metals undergo a preparation process before the brazing can commence. Amalco. amalco is a manufacturer of deep drawn and hydroformed metal parts and has served many industries since they were founded in 1910 in mountainside, new jersey. they specialize in a broad range of metal forming and joining processes, including dip brazing, and serve several different industries, including food beverage, electronics. Electroplating is primarily a surface treatment process, enhancing surface characteristics without altering the base material's properties. in contrast, vacuum brazing is a joining technique, focused on creating strong, integral bonds between different components. the choice between electroplating and vacuum brazing depends on the specific. The advantages of joining metals by brazing are that dissimilar metals and parts having a thin section can be joined easily. brazing is used for the fastening of pipe fittings, and tanks, credible tips on tools, radiators, heat exchangers, and the repair of castings. read also: types of fasteners and their uses.

Brazing Manufacturing Process At Freddy Frederick Blog Electroplating is primarily a surface treatment process, enhancing surface characteristics without altering the base material's properties. in contrast, vacuum brazing is a joining technique, focused on creating strong, integral bonds between different components. the choice between electroplating and vacuum brazing depends on the specific. The advantages of joining metals by brazing are that dissimilar metals and parts having a thin section can be joined easily. brazing is used for the fastening of pipe fittings, and tanks, credible tips on tools, radiators, heat exchangers, and the repair of castings. read also: types of fasteners and their uses. The brazing process also lends itself to applications in which manually fixtured and loaded assemblies are carried through a brazing oven by a conveyor as part of an in line process, or brazed in batches. ultimately, the best approach for any given application is largely a function of the materials involved and production volumes. Brazing is a process that joins two or more metal surfaces by letting molten metal flow into the joint. the filler metal has a lower melting temperature than the parts to be joined to keep the workpieces from melting. although brazing is one of the oldest joining methods, it is still used today for a good reason. key takeaways. brazing joins.
Comments are closed.