Automatic Visual Inspection For Precision Machining Parts
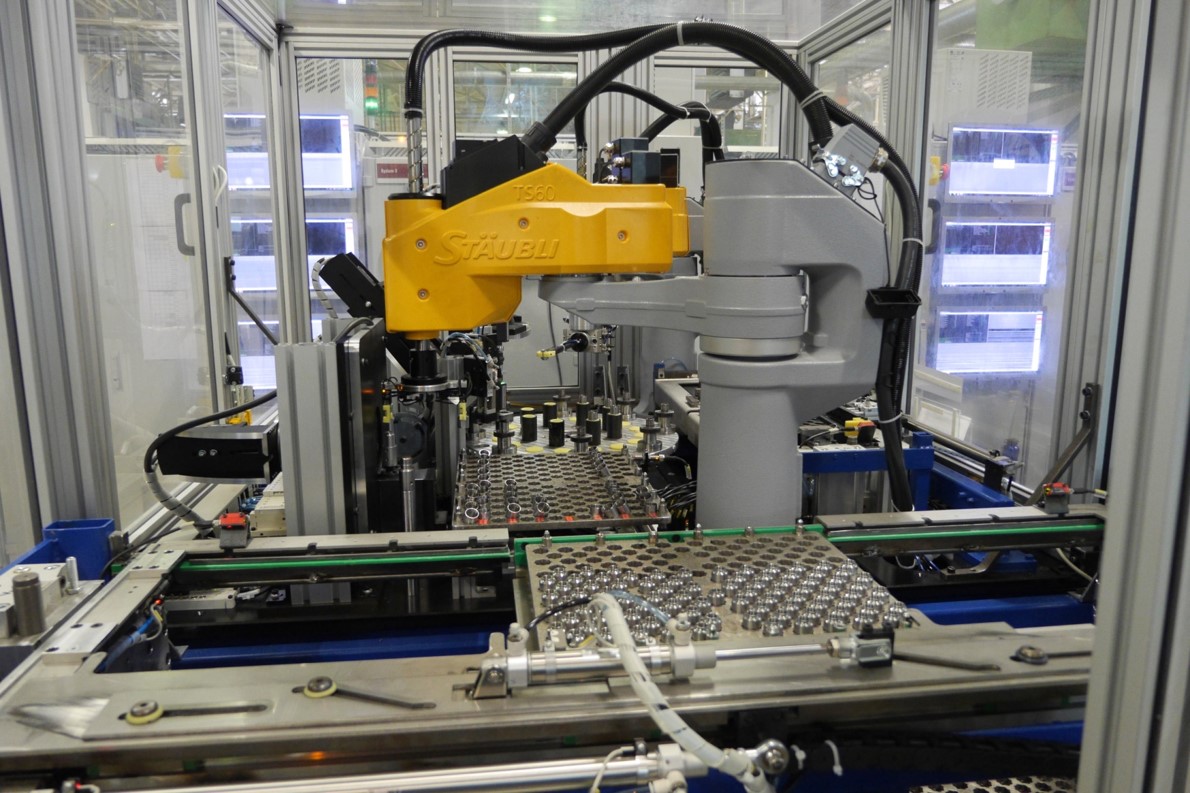
Automatic Visual Inspection For Precision Machining Parts Automatic visual inspection in precision machining. october 11th, 2022. with cnc precision machining the last part to come off a machine should be identical to the first part. despite their impressive repeatability though, inspection is still necessary. it verifies that the first part conforms to the print, and it finds defects if anything. The inspect.assembly is designed for integration directly into the production line, with an adjustable frame to accommodate conveyer heights from 525 mm to 950 mm. the total operating footprint is within 1860 mm (h) x 800 mm (w) x 700 mm (d), occupying the same physical footprint as a human inspector on the line.

Advanced Automated Visual Inspection Systems For Industrial All about automated visual inspection systems. posted february 10, 2021. every manufacturer requires quality control to ensure its products leave the factory without defects. this is especially true for producers of smaller precision components. today’s key element in quality assurance (qa) is automated visual inspection systems. This 100% automated inspection provides to our production department a significant amount of data used to control our machining processes. capabilities for most key characteristics are derived from these inspections and guarantee a close follow up of any deviation. mechanical parts produced in djc precision cnc machning facilities are delivered. Part of the reason 55th cirp conference on manufacturing systems automated visual inspection of manufactured parts using deep convolutional neural networks and transfer learning karsten weiher*a, sebastian riecka, hannes pankratha, florian beussa, michael geista, jan sendera, wilko flueggea,b afraunhofer institute for large structures in production engineering igp, albert einstein str. 30. Though there is an abundance of literature in the area of automatic visual inspec tion for specific domains (e.g., solder joints, printed circuit boards, light bulb filaments, etc.), literature on inspection systems (specifically cad based) for gen eral machine parts is hard to come by. requicha [req83] was the first to lay down.

Automated Visual Inspection Machines From Machine Vision Inspection Part of the reason 55th cirp conference on manufacturing systems automated visual inspection of manufactured parts using deep convolutional neural networks and transfer learning karsten weiher*a, sebastian riecka, hannes pankratha, florian beussa, michael geista, jan sendera, wilko flueggea,b afraunhofer institute for large structures in production engineering igp, albert einstein str. 30. Though there is an abundance of literature in the area of automatic visual inspec tion for specific domains (e.g., solder joints, printed circuit boards, light bulb filaments, etc.), literature on inspection systems (specifically cad based) for gen eral machine parts is hard to come by. requicha [req83] was the first to lay down. Thus, replacing the human visual inspection with a fully automatic system will normally increase the accuracy of defect detection and reduce costs [4]. when properly applied, machine vision can provide accurate and real time inspection [5] and this technology has been widely used for metal surface quality control. Our robotic automated visual inspection solutions detect surface defects (nicks, scratches, tooling marks…) and apply your specific inspection criteria depending on the location on the part. defects as small as 0.125 mm can be detected, depending on the surface quality. to reach such capability, our team has developed algorithms specifically.
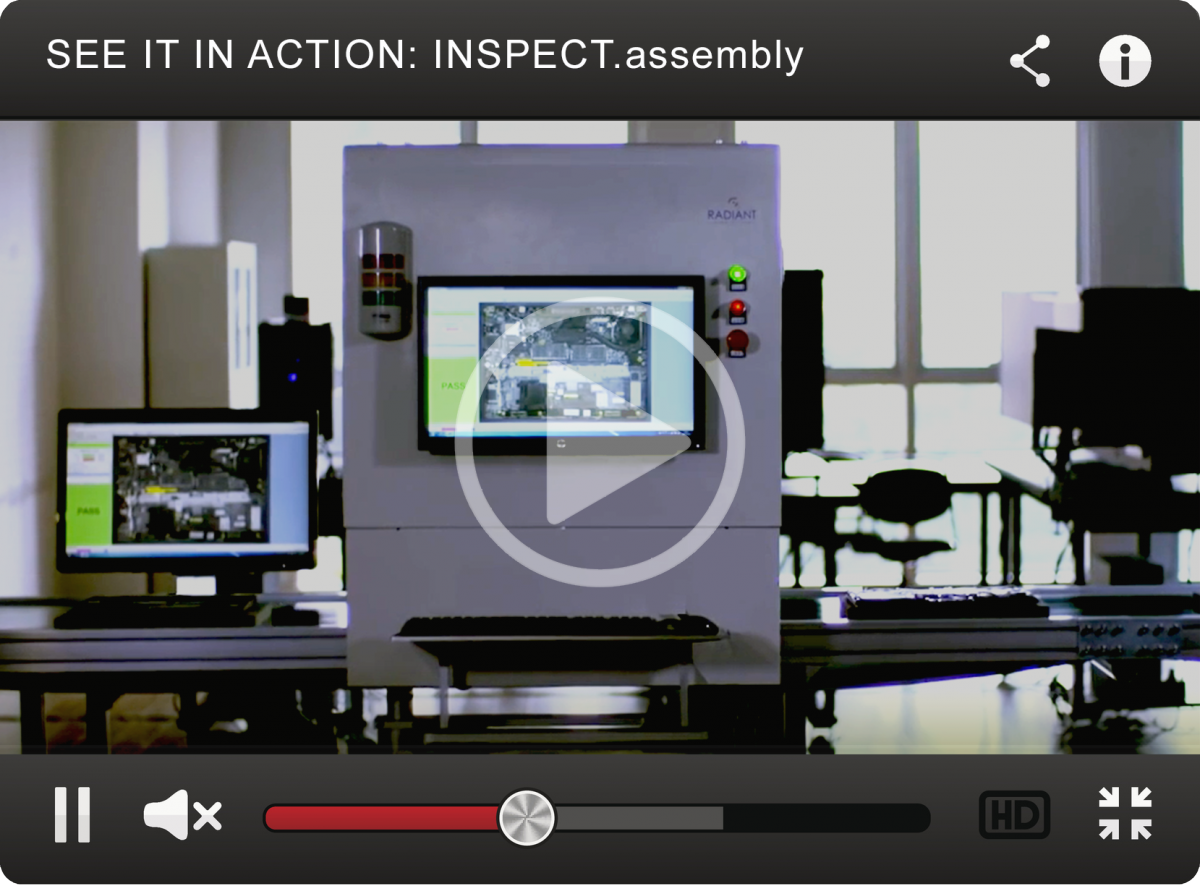
Inspect Assemblyв ў Automated Visual Inspection Station Radiant Vision Thus, replacing the human visual inspection with a fully automatic system will normally increase the accuracy of defect detection and reduce costs [4]. when properly applied, machine vision can provide accurate and real time inspection [5] and this technology has been widely used for metal surface quality control. Our robotic automated visual inspection solutions detect surface defects (nicks, scratches, tooling marks…) and apply your specific inspection criteria depending on the location on the part. defects as small as 0.125 mm can be detected, depending on the surface quality. to reach such capability, our team has developed algorithms specifically.

Automated Visual Inspection Of Machined Parts Djc
Comments are closed.