Automated Visual Inspection Avi For Manufacturing
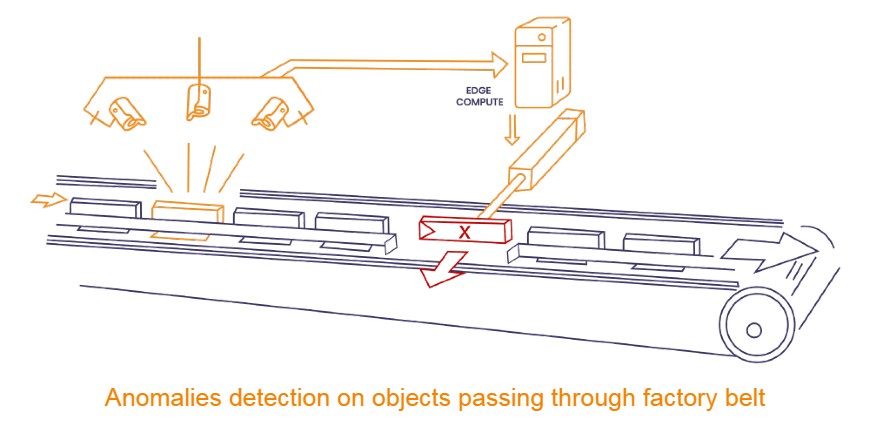
Automated Visual Inspection Avi For Manufacturing Ai: ai, especially deep learning algorithms, provides the automation vision inspection system with powerful image understanding and analysis capabilities. it can identify complex and minute defects — achieving highly accurate quality control. rgbd: rgbd technology combines color images and depth information to enhance automated systems with. Automated visual inspection (avi) it entails analyzing items on the production line for quality control purposes. visual inspection may also be used to examine the different equipment in a manufacturing plant, such as storage tanks, pressure vessels, pipelines, and other equipment, both internally and externally.

Advanced Automated Visual Inspection Systems For Industrial Automated visual inspection refers to the use of specialized cameras, sensors, and supporting computer systems and algorithms to examine products or components for defects or deviations from desired specifications. this process, often part of a larger quality control system, relies on visual data to make assessments, substituting human visual. Quality assessment in industrial applications is often carried out through visual inspection, usually performed or supported by human domain experts. however, the manual visual inspection of processes and products is error prone and expensive. it is therefore not surprising that the automation of visual inspection in manufacturing and maintenance is heavily researched and discussed. the use of. Overview. automated visual inspection (avi) is a quality control method in which products are automatically analyzed for inconsistencies through machine vision technology and artificial intelligence. traditionally, quality control in manufacturing is performed through manual inspection. this visual inspection can have drawbacks. Quality control, productivity, and efficiency through the power of automation. an automated vision inspection system (avi), also known as an automatic machine vision system or optical inspection machine, is a sophisticated machine that uses advanced imaging technology such as cameras, sensors, and image processing software to automatically.

Automated Visual Inspection Avi Of Displays Solutions For Reducing Overview. automated visual inspection (avi) is a quality control method in which products are automatically analyzed for inconsistencies through machine vision technology and artificial intelligence. traditionally, quality control in manufacturing is performed through manual inspection. this visual inspection can have drawbacks. Quality control, productivity, and efficiency through the power of automation. an automated vision inspection system (avi), also known as an automatic machine vision system or optical inspection machine, is a sophisticated machine that uses advanced imaging technology such as cameras, sensors, and image processing software to automatically. Ensuring product first class while optimizing manufacturing tactics is a steady project. this is wherein automated visual inspection (avi) structures come into play. avi structures leverage modern era, including artificial intelligence and system mastering, to carry out visual inspections with incredible accuracy and velocity. In the semiconductor industry, automated visual inspection aims to improve the detection and recognition of manufacturing defects by leveraging the power of artificial intelligence and computer vision systems, enabling manufacturers to profit from an increased yield and reduced manufacturing costs. previous domain specific contributions often utilized classical computer vision approaches.
Comments are closed.