Lean Tools Developing Standard Work In 6 Steps Skil Global Business
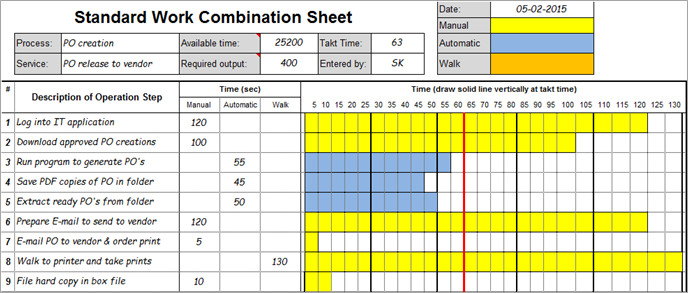
Lean Tools Developing Standard Work In 6 Steps Skil Global Business Firstly, identify the operation or process step that needs standard work documentation. assign duties to the different team members and leader. secondly, schedule a video shoot of the operation as it takes place – right from the start to the end. thirdly, review the video for time and motion studies with the team. Find out the 2 key result areas which depend upon your ability to implement lean effectively! business, customer, kaizen, lean, lean implementation, problem solving, project execution, six sigma. there are 6 steps to implement lean effectively in an organization. lean is pivotal to your company's efficient performance and success!.
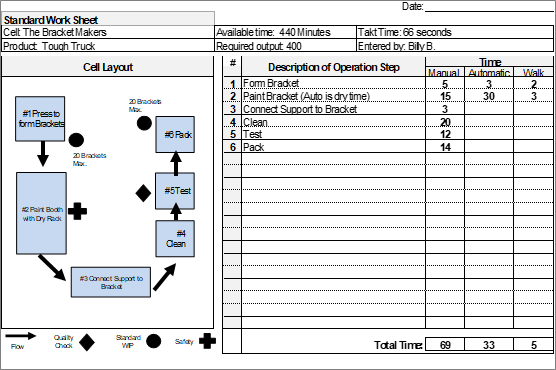
Lean Tools Developing Standard Work In 6 Steps Skil Global Business It is difficult to say which lean tool you should apply first. this is because it depends on your company’s level of maturity. for instance, ‘standard work’ should go first in some companies. on the other hand, perhaps 5s would suit others better. therefore, it is crucial to use your judgment. Standard work instructions (swis) are vital tools in business and industry, offering clear and detailed guidance on executing specific tasks. tailored to suit various tasks, machines, or work environments, swis are particularly beneficial for processes demanding consistent and reproducible outcomes. in environments like manufacturing, where precision is key, swis play a crucial role in. Standard work is one of the fundamental disciplines of the toyota production system (tps) and lean manufacturing. also called standardized work, standard work is key to maintaining stability, solving problems effectively and scientifically, and kaizen (continuous improvement). standard work definition: the best known and demonstrated method for. The confusion is semantic as well, because the word standard lends itself to a few interpretations: it could be seen as referring to a “work standard” (we start at 9am, we all wear the same boots, a break lasts for 10 minutes, and so on), to a sop (a standard operating procedure, which is the depiction of how a process flows) or to.
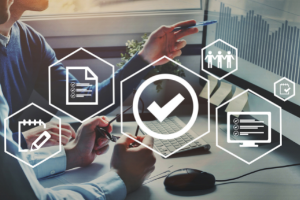
Lean Tools Developing Standard Work In 6 Steps Skil Global Business Standard work is one of the fundamental disciplines of the toyota production system (tps) and lean manufacturing. also called standardized work, standard work is key to maintaining stability, solving problems effectively and scientifically, and kaizen (continuous improvement). standard work definition: the best known and demonstrated method for. The confusion is semantic as well, because the word standard lends itself to a few interpretations: it could be seen as referring to a “work standard” (we start at 9am, we all wear the same boots, a break lasts for 10 minutes, and so on), to a sop (a standard operating procedure, which is the depiction of how a process flows) or to. Overall, standard work plays a vital role in the success of lean methodology. by establishing clear processes and procedures, organizations can streamline their operations, reduce waste, and improve overall efficiency. standard work serves as a foundation for continuous improvement and ensures consistency and quality in business operations. Conclusion. practical lean standard work is a foundation element of lean manufacturing methodologies. without it, the gains made from the other lean tools, such as visual management, 5s, work cells, flow production, and continuous improvement, will only be short lived. standard work prevents the slide back to less efficient work practices.

Lean Six Sigma Principles And Tools And Their Applications Overall, standard work plays a vital role in the success of lean methodology. by establishing clear processes and procedures, organizations can streamline their operations, reduce waste, and improve overall efficiency. standard work serves as a foundation for continuous improvement and ensures consistency and quality in business operations. Conclusion. practical lean standard work is a foundation element of lean manufacturing methodologies. without it, the gains made from the other lean tools, such as visual management, 5s, work cells, flow production, and continuous improvement, will only be short lived. standard work prevents the slide back to less efficient work practices.
Comments are closed.